A cone crusher is a key piece of industrial equipment used in various industries such as mining, construction, and aggregate production. It is primarily used to crush hard and abrasive materials, making it especially effective in applications involving rocks, ores, and minerals. Cone crushers are widely utilized due to their high efficiency, productivity, and the consistency they provide in material output.
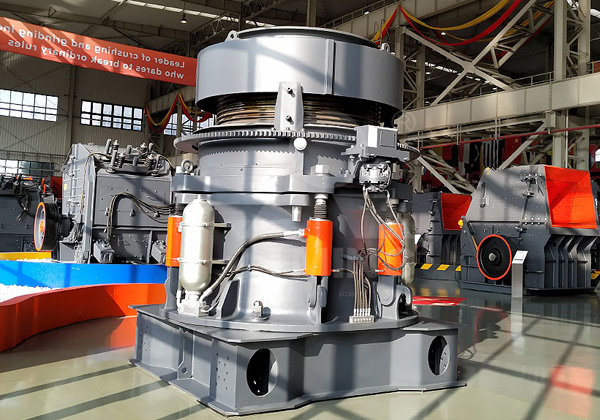
Key Components
- Mantle and Concave: These two components form the crushing chamber. The mantle is attached to the crusher’s spindle and is the part that gyrates, while the concave forms the outer surface where material is crushed.
- Main Shaft: The shaft holds the mantle and moves it in an eccentric motion to generate crushing pressure.
- Hydraulic System: Modern cone crushers often come equipped with a hydraulic system for adjusting the settings. This system allows for the adjustment of the crusher’s closed-side setting (the minimum distance between the mantle and concave), which directly impacts the final product size.
- Consistency in Output: Cone crushers offer consistent particle size output, which is crucial for industries requiring uniform material sizes, such as road construction and concrete production.